August 6th, 2024
The ability to mass produce complex plastic parts with high precision and efficiency is one of the main benefits of injection molding. However, the proficiency and effectiveness of it depend heavily on the proper upkeep of equipment and processes. Therefore, fostering robust maintenance procedures is crucial to the longevity, reliability and performance of injection molding machines and molds.
Equipment Longevity
A primary objective for developing proper service practices in injection molding is to extend the lifespan of any related apparatus. The machines and molds used are significant investments and their premature failure can lead to substantial financial losses. Regular care helps identify and address potential issues before they escalate into major problems. By implementing a preventive maintenance schedule, manufacturers can replace worn-out components, lubricate moving parts and ensure that all systems function optimally. This active approach not only prolongs the life of the equipment but also minimizes the risk of unexpected breakdowns that can disrupt production.
Product Quality
The worth of the final product is directly influenced by the condition of the injection molding equipment. Any deviation from the specified parameters, such as temperature, pressure or mold alignment, can result in defects like warping, flash, sink marks or short shots. Consistent and thorough conservation habits help warrant accuracy throughout the entire process. Regular calibration of sensors, inspection of molds for wear and tear in addition to cleaning of nozzles/vents make sure that everything operates within the desired specifications. This, in turn, translates to an end result of superior parts with minimal flaws, subsequently meeting customer expectations and lessening the need for rework or scrap.
Operational Efficiency
Optimal performance is a fundamental factor in the success of every premier manufacturing business. Downtime due to neglect or unscheduled repairs can greatly impact working schedules and delivery timelines. Developing and adhering to servicing routines can elevate every aspect of a facility. Preventive control reduces the likelihood of unexpected malfunctions – well-maintained equipment means peak performance, reduced cycle times and less energy consumption. This generates higher output and lower costs, enhancing the overall outcome.
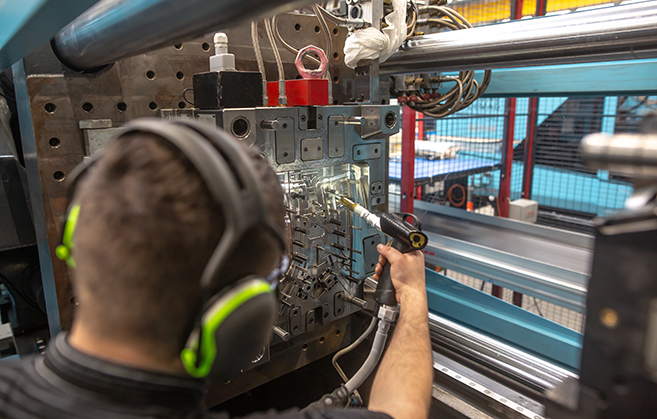
Cost Savings
Proactive safeguarding could reduce expenses. While there may be an upfront outlay to develop and execute a program, the return is ultimately positive. Preventive measures will curtail issues before they occur. Replacing a worn-out seal or bearing during a routine check is far less expensive than dealing with breakdowns that require extensive restoration or even a new purchase. Furthermore, abating interruption and advancing operational capability lowers labor costs and improves resource utilization. By avoiding the risk for defects and warranting consistent production, companies will diminish spending while expanding profit margins.
Safety and Compliance
Injection molding involves high pressures, temperatures and the use of potentially hazardous materials. Promoting the safety of workers and compliance with industry regulations is vital. Well-developed strategies play an essential role in offering a secure environment. Regular safety inspections including emergency stops, guards and interlocks facilitate a hazard-free zone. Compliance with regulations not only protects employees but averts legal and financial consequences. Good equipment maintenance assures that specific standards are met.
Sustainability
Managing sound ecological procedures is becoming increasingly important in modern manufacturing. Injection molding production may pose a recognizable environmental concern due to noticeable energy consumption, material waste and emissions. Alert planning enhances performance in all related areas, contributes to viable efforts in easing power usage and decreases scrap. Well-kept machines function more efficiently, using less power and outputting fewer defective parts that would otherwise end up as waste. Periodic inspection can detect and address leaks that could bring about environmental contamination. By incorporating mindful practices into production, manufacturers can contribute to environmental protection and align themselves with global sustainability goals.
Developing Effective Procedures
To develop an appropriate agenda for injection molding, manufacturers should consider the following key steps:
- Assessment and Planning: Conduct a thorough assessment of the equipment and processes to identify critical components and potential failure points. Design a comprehensive guide that outlines the frequency and scope of required activities.
- Documentation and Standardization: Create detailed documentation of compulsory logistics, including step-by-step instructions, checklists and safety guidelines. Standardize these procedures across all equipment and facilities to ensure consistency.
- Training and Skill Development: Provide training for personnel to make sure they have the necessary skills and knowledge to perform tasks correctly. Regularly update training criteria to keep up with technological advancements and industry best practices.
- Preventive Maintenance Schedule: Construct a solid timetable based on manufacturer recommendations, equipment usage and historical data. Include routine examinations, lubrication, calibration and component replacements.
- Monitoring and Data Analysis: Implement monitoring systems to track equipment performance and collect data on corresponding activities. Analyze this information to identify trends, optimize schedules and make informed decisions.
- Continuous Improvement: Regularly review and update procedures based on feedback from personnel and operational stats. Continuously seek opportunities that improve the organization and validity of these methods.
For these reasons and more, having stringent check-ups are vital to our industry. Everything from equipment longevity, active management, product quality and identifiable savings are all directly related with unwavering adherence to such processes.
By investing in comprehensive maintenance programs, manufacturers can ensure the reliable and efficient running of their injection molding equipment, leading to improved productivity, reduced downtime and enhanced profitability. This is not just another expenditure, it’s a strategic move that pays dividends in the form of increased excellence and long-term business success.