June 6th, 2023
The medical plastic injection molding industry has witnessed remarkable growth over the years, transforming the landscape of healthcare. It involves the manufacturing of a variety of complex and precise medical devices and components using advanced molding techniques. This expansion has been driven by many factors including high-tech advancements, increased demand for medical devices and a focus on cost-effective and efficient processes. Below, we will delve into some key factors contributing to the growth of medical molding enterprises, and its nearly $100M industry. Let’s take a closer look at its significant impact on healthcare in general.
Technological Progressions
The medical molding industry has thrived on industrial innovations that have altered its production methods. Advanced techniques like injection molding, blow molding and micro-molding have enabled the assembly of intricate medical devices with meticulous consistency. Additionally, the integration of robotics, automation and 3D printing has streamlined manufacturing, reduced costs and improved product quality.
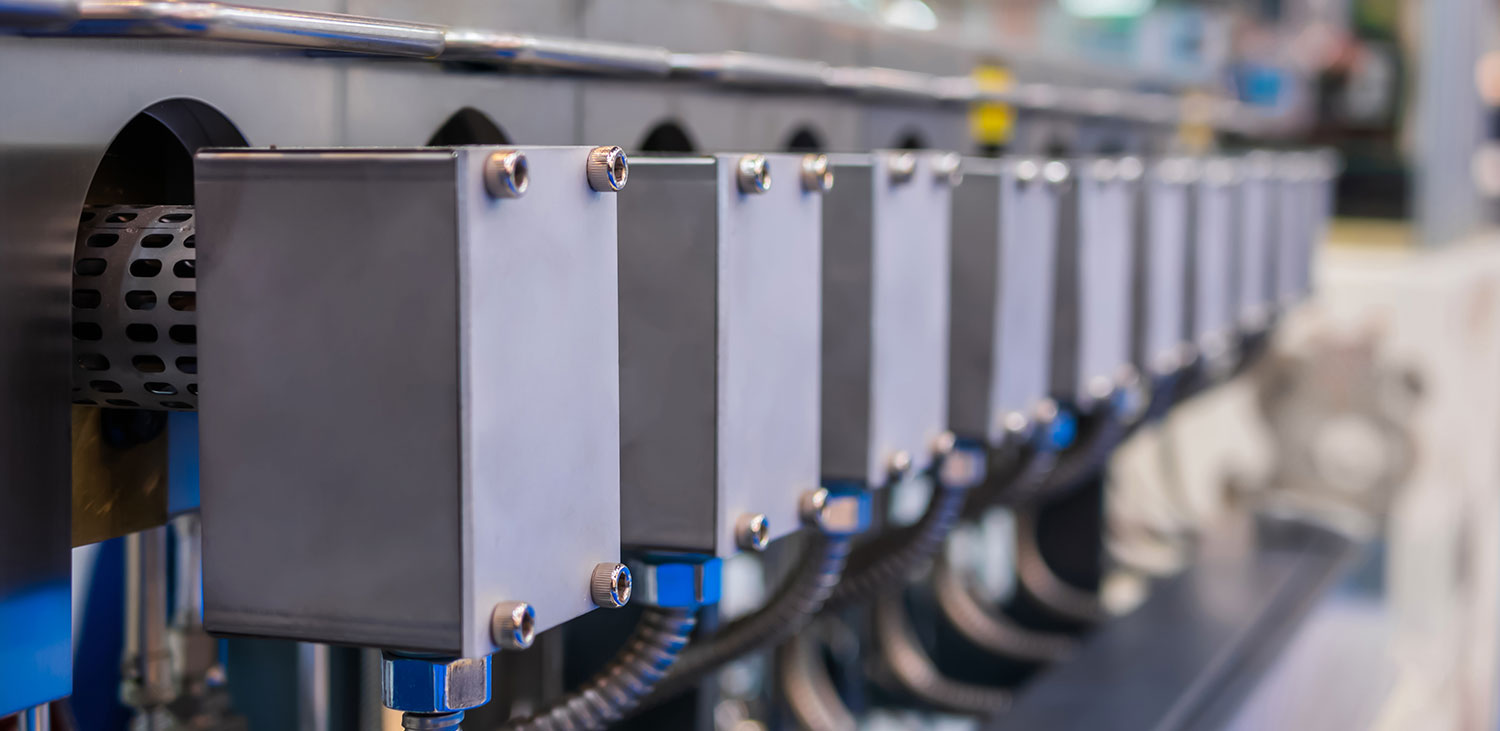
Rising Demand for Medical Devices
The increasing global population, aging demographics and modern contributions to this vital field has fed the demand for improved medical apparatuses. From surgical instruments and implants to drug delivery systems and diagnostic tools, medical molding plays a crucial role in meeting these needs. The ability to generate sophisticated and customized components quickly has allowed medical design manufacturers to innovate and develop cutting-edge solutions.
Regulatory Compliance
The industry operates under stringent regulatory guidelines to ensure the safety and efficacy of medical appliances. Adherence to regulations such as ISO 13485 (Quality Management System for Medical Devices) and FDA guidelines is essential. Developers who invest in state-of-the-art molding and maintain strict quality control procedures gain a competitive edge by meeting regulatory standards effectively.
Efficiency and the Bottom Line
Medical-grade molding often translates to lower expenditures when producing larger volumes of equipment/parts to be used in this important field. The high productivity, repeatability and low waste that is associated with superior injection mold making practices results in reduced outlay. Additionally, modernizations like multi-cavity molds and automation have further ramped-up proficiency, enabling faster production cycles and shorter time-to-market for new products.
Material Innovations
There have been major advancements in material science, with the development of biocompatible and sterilizable products. These parts ensure tolerance with the human body and maintain adequate integrity under various sterilization methods. Medical-grade polymers, such as PEEK and ABS, have become popular choices for the manufacturing of such devices due to their superior mechanical properties and organic nature.
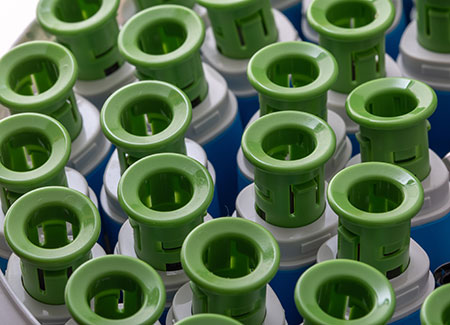
Miniaturization and Complex Designs
Medical equipment is increasingly becoming smaller and more intricate. This trend has been embraced, enabling the production of multifarious designs and miniaturized components. Micro-molding techniques, such as insert molding and overmolding, have facilitated the creation of miniscule but high precision tools, allowing for marginally invasive procedures and improved patient comfort.
Customization and Personalization
Patient-specific care and personalized medicine have gained momentum, and medical molding has taken advantage of this shift. With advancements like 3D printing and computer-aided design (CAD), these devices can now be customized to match personalized patient requirements. Individually tailored prosthetics, orthopedic implants and dental aligners are just a few examples of how medical molding has transformed patient care.
Industry Collaboration and Partnerships
The impressive growth of the medical molding industry has been accelerated by collaborations between manufacturers, material suppliers and healthcare providers. This cooperation fosters innovation, encourages knowledge exchange, and drives fresh developments. Such partnerships enable R&D personnel to gain insights into specific needs, ensuring the production of made-to-order effective medical equipment.
Global Market Expansion
The demand for medical devices extends beyond regional boundaries. The medical molding industry has capitalized on this global market expansion, with manufacturers establishing their presence in various countries. Access to emerging markets, such as Asia and Latin America, provides multiple opportunities for this industry and allows them to grow geographically as well.
While these are many of the largest factors contributing to the ever-growing medical molding industry, there are still many more influences. This sizeable market touches various other areas and therefore is revolutionizing both molding and healthcare.
Here at Slide, we look to continue monitoring its progression and make sure our products are able to add efficiency to every step of the process.