July 23rd, 2024
As injection molding advances to create stronger and more durable materials, the demand for high-temperature resins has surged across various industries. These formulations offer superior performance characteristics making them ideal for applications in the automotive, aerospace, medical and electronics sectors. However, their use introduces some new challenges, particularly in the maintenance and cleaning of injection molding equipment.
Hi-temp resins are engineered to withstand severe conditions and maintain their integrity under extreme heat. This proves them to be invaluable in treatments where traditional plastics would fail. Some of the most sought-after mixes include:
(PEEK) – Polyetheretherketone is a semi-crystalline thermoplastic polymer with a chemical structure (-C6H4-O-C6H4-O-C6H4-CO-) like PEI.
(Ultem®) – A brand name developed in 1982 by General Electric Company for (PEI) – polyazridine a synthetic amorphous thermoplastic polymer holding a complex chemical network.
(PPS) – Polyphenylene sulfide is a crystalline heat resistant polymer that has a simple chemical make-up of benzene and sulfur.
Below is a list of positive attributes related to such hi-temp resins.
- Thermal Stability: Withstands elevated temperatures without degrading, making them suitable for components exposed to high heat.
- Mechanical Strength: Possesses excellent tensile strength, impact resistance and dimensional stability.
- Chemical Resistance: Counteracts chemical attacks from opposing solvents/acids and bases.
- Durability: Maintains hi-temp endurance with a longer lifespan.
Given these advantages, it’s no surprise that industries are increasingly opting for a transition to this type of resin to enhance the performance and longevity of their parts.
Without a doubt, stronger resins bring about numerous benefits, but also can carry unique obstacles during injection molding production. One of the more significant issues is the building up of residue in molding machinery. Over time, this accumulation leaves behind material, deposits, rust and more. Problems ensue that can lead to defects in the molded pieces, increased downtime for cleaning, and ultimately, higher operational costs. To address these hindrances, a specialized purging compound is essential.
Purging agents are formulated to clean the injection molding apparatus by removing residual resins, contaminants and deposits. Applying a purging composite is critical for several reasons:
- Maintaining Product Quality: Regular purging certifies that the molded parts are free from defects caused by pollutants.
- Prolonging Equipment Life: Removing debris and preventing corrosion helps extend the lifespan of the molding equipment.
- Reducing Downtime: Effective purging minimizes the time required for cleaning, allowing for quicker changeovers and higher productivity.
- Enhancing Efficiency: A clean system operates more efficiently, reducing energy consumption and improving cycle times.
Considering the harsher processing climate and the unique complications posed by hi-temp resins, a standard purging agent may not suffice.
Slide Products has developed a Hi-Temp Purge Compound specifically designed to tackle the difficulties associated with purging engineering-grade resins. Here are some areas in which the Slide’s product excels:
- Chemically Reactive Formula: Unlike abrasive purging agents, Slide’s Hi-Temp Purge is chemically reactive, meaning it interacts with the residues at a molecular level to break them down. This guarantees thorough treatment without causing wear and tear on the equipment.
- Non-Abrasive: The inherent non-abrasive nature protects screws, barrels and hot runners from damage, preserving precision and longevity.
- Extreme Heat Tolerance: When used in conjunction with proper guidance from our factory experts, Slide’s Hi-Temp Purge Compound is effectual and safe at up to and exceeding 1,000°F.
- Effective Contaminant Removal: The compound quickly eradicates burnt matter, color hang-ups, resin sediments, black specks and rust. An extensive cleansing property makes sure devices are free from pollutants that could compromise quality.
- Safe and Easy to Use: Food grade with virtually no odor or smoke, non-toxic to handle and decreases hazardous waste. Within a simplified maintenance program, it also reduces the need for a manual concentrated effort.
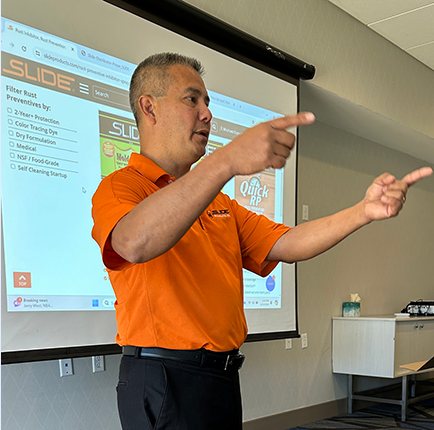
Juan Grino, Slide factory rep and purging expert explains, “We pride ourselves in assisting our customers and helping to customize product offerings that fit individual needs. This is why we are always available to offer a free purging consultation to ensure you're getting the best possible solution in any injection molding environment.”
In conclusion, the rising popularity of hi-temp resins chosen for their outstanding performance and durability has brought on a wide range of new hurdles encompassing the industry. For that reason, Slide created the Hi-Temp Purge Compound as a comprehensive solution to these kinds of obstacles. Its chemically reactive, non-abrasive formula, high-temperature resilience and effectiveness in removing various impurities make it an indispensable tool for manufacturers. By incorporating this formulation into their maintenance routines, we assist injection molding professionals to foster progress and optimize their operations.