June 20th, 2023
One of the best ways for manufacturers to produce their products more efficiently and at lower costs is by utilizing small plastic parts. Recent technology has allowed injection molders to create strong, flexible and durable components from polymers instead of using metal. This smart changeover is saving thousands of dollars and helping processes become faster with less room for error.
When it is necessary to create diminutive cuts with intricate designs, Injection molding is the preferred technique. Under this manufacturing practice, polymers are melted down and introduced into a mold to create various shaped pieces. Its very nature provides the capability to completely customize molds. Outputs are generated faster and more precisely than other manufacturing methods, including machining or casting.
While decreased cost and increased efficiency are two major benefits for use of small plastic parts in manufacturing, there’s more to consider.
Lightweight
The composition of carbon and hydrogen makes plastic much lighter than metal. With lower weight, they are easy to transport and less expensive to ship. Industries such as automotive and aerospace have taken advantage of this benefit as weight is often a concern in their processes.
Corrosion Resistant
Unlike metal, plastic is highly corrosion-resistant and will not rust. Components stay unharmed even when exposed to harsh chemicals or salt water. Plastics tend to be ideal for environments where deterioration would be a concern such as in food processing or medical applications.
Non-Conductive
Plastic is a good insulator and therefore does not conduct electricity. When safety is an issue, plastic is often the way to go to ensure limitation of injuries or accidents. Electronic devices and enclosures now utilize more plastic than ever to take advantage of this asset.
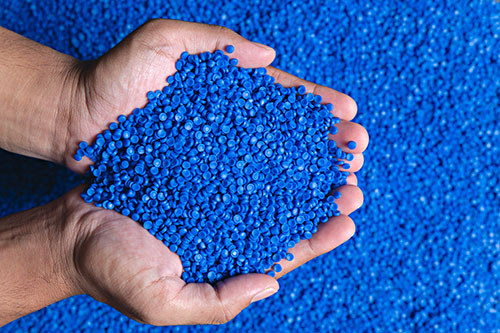
More Flexibility
Small plastic parts can be flexible and therefore designed to fit into tighter, more irregular spaces. This characteristic makes plastic stand out significantly from metal which has very little adaptability to conform in these circumstances.
Stronger than Metal
Because plastic can be custom made and is typically stronger than other materials, specific properties such as impact resistance keep polymers rigid and stable in many applications. Industries such as automotive and construction have determined this to be true and now turn to synthetics to fulfill their needs.
Easy to Recycle
Plastic is one of the easiest materials to recycle making it an eco-friendly, low-waste selection – It melts down without difficulty. Repurposing plastic into new products is simple and helps to conserve resources and refurbish leftovers. That is certainly something to consider when looking to keep operations as sustainable as possible.
Design Freedom
Plastic parts can be molded into any shape and color and are very aesthetically appealing. This gives manufacturers design freedom along with a wide range of possibilities. In addition, it is available textured or finished to provide varied and interesting looks.
For these reasons and more, manufacturers are turning to injection molding to produce small plastic parts for their production requirements. With so many benefits, it’s often chosen to ensure durability and quality. This growing trend is something we expect to continue and be expanded on in the future.