April 9th, 2024
Minimizing scrap is often one of the most critical matters with respect to ensuring profitability within the injection molding industry. While defects in parts can originate from many factors, neglecting the speed and time settings during the molding process tends to act as the main determinant of production inefficiencies. Therefore, it is important to understand the tactics that can be used to prevent issues and optimize operations for enhanced productivity and profit.
Injection Speed
Injection speed plays a pivotal role in the quality of the molded parts. While commonly used, a one-size-fits-all approach to injection speed often falls short due to the complex nature of the flow navigating through the runner system and cavity. Instead, each stage encompasses its own rate considerations to best maximize manufacturing outcome:
Initial Fill: Within this phase, excessively high velocity potentially creates splay or jetting, whereas a slower pace might result in overpacking and sticking in areas with detailed features like ribs or tabs. Therefore, a middle ground is necessary for a controlled fill.
Throughout the Mold: High speeds in the mold can lead to incomplete filling or poor welding of the plastic around small cavities, possibly triggering burns or trapped gas toward the end of a run. On the other hand, slow speeds risk short shots from inadequate gas escape.
Adopting multiple speed variations based on the specific phase of the filling process can significantly mitigate these issues. Furthermore, analyzing injection profiling allows for targeted speed adjustments to maintain part quality.
Screw Recovery
The integrity of the molding process is also influenced by the screw recovery time, which is inversely related to its RPM. For this reason, a balance between screw rotation time and the cooling timer is imperative. Optimal screw recovery occurs 1.5 to 2 seconds before the cooling timer concludes, safeguarding consistent cycle times and material soundness. Conversely, overly brisk screw rotation can compromise material mixing, while excessive recovery measures disrupt operational dependability.
Post-Rotation Decompression
Post-rotation decompression speed is also very important, especially considering material viscosity. Rapid decompression can introduce splay, whereas too gradual a pace might prevent the check ring from seating correctly, affecting shot size uniformity.
Large investments are being put into superior-performance polymer research which will translate to additional treatments across numerous industries. Though currently representing only 1% of total plastics utilization, materials are needed at a rate faster than the market can bear.
Mold and Ejector Speeds
Mold opening and closing speeds directly influence cycle times, with faster speeds favoring consistency. However, the complexity of the mold may hinder such rates affecting both part quality and mold longevity. Similarly, ejector speed should be optimized to swiftly discharge parts without compromising removal regularity or causing damage.
Cooling
The cooling stage significantly affects part dimensions and structural integrity. Parts removed too early from the mold might shrink excessively or warp, underlining the importance of calibrated cooling intervals. Instead, timing should be tailored so there is an adequate leeway for proper shrinkage. This essential procedure should render related dimensional specifications to parts and prevent a delay in the cycle.
While understanding the properties of speed and time settings is vital, facilitating these strategies can further curtail defects:
Dynamic Monitoring and Adjustment: Continuously monitor production for any signs of imperfections and adjust speeds and times as needed. Advanced sensors and real-time analytics could also be used for more accuracy.
Comprehensive Process Simulation: Utilize simulation software to predict and mitigate potential defects by experimenting with different speed and time regulation in a virtual environment before actual production.
Regular Maintenance and Calibration: Ensure that all equipment is regularly maintained and calibrated to operate at proper speeds and times, maintaining products to their ultimate standards.
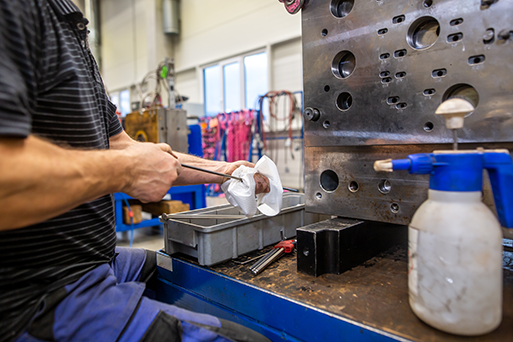
Staff Training: Equip staff with the knowledge and authority to moderate and fine-tune speed and time settings as required, fostering a culture of quality and responsiveness.
Navigating the intricacies of injection molding speed and time settings presents challenges but a deep understanding paired with strategic preventive methods can drastically increase production efficacy and product excellence. Here at Slide, we always aim to help our customers achieve manufacturing distinction through Top Tier products and techniques. Reach out to an expert to learn how we can improve your molding speed today!