June 4th, 2024
A dedicated greasing program is an underutilized, proactive resource across all machining industries. When the Slide team walks onto the floor of any factory, we usually find a multitude of greasing compounds on some designated shelf. Most related technicians don’t realize that taking ‘A’ grease + ‘B’ grease = sticky parts that could potentially result in considerable downtime.
Moving mold components typically have tight tolerances that require lubrication to perform at their best. Once gumming starts, the linesperson will notoriously “attack” the mold with a quick- fix greasing spray which will only provide short-term relief. However, the problem is that by mixing two variations – a petroleum-based grease with a synthetic one – makes both less effective. The outcome is not good as bleed out, parts contamination, altered optimal temperatures and a “tacky” feel often follow. It’s important to attend to a poorly greased machine while utilizing the right product as soon as possible. Otherwise, you will increase the likelihood of the machine seizing and it would be akin to operating it dry.
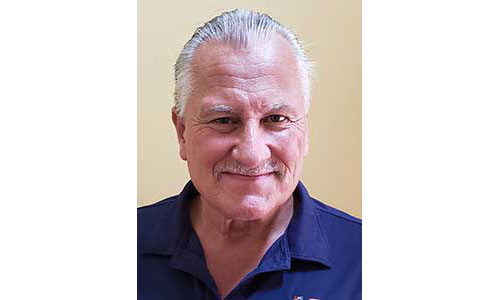
Jeff Lewis, Slide’s factory rep and master of mold releases, recalls an unpleasant situation in Mexico City where the machine became unstable and bounced due to poor greasing, and subsequently it took five hours to resolve.
“I remember sitting on the floor with a polishing stone, re-straightening and re-polishing the pins so that the machine would be up for production in the morning.”
The machine was shipped without being properly lubricated and had frozen up when started. This caused ejector pin bending and therefore damaged parts which needed to be removed, hand polished then straightened before everything could be correctly greased and prepared for a tradeshow the following day.
Proactive Greasing System Guide
- A preventative maintenance plan should be in place for each facility. Preliminary testing is necessary so that you know how many cycles can sequence before reapplication of the grease is required.
- Communication between the supervisory shop and processing crew is vital. If the back half of the mold is lubricated properly, but the front end of the unit is coated in a different formula, problems will likely occur. Be sure that one – and only one – grease is readily accessible in both the shop and next to each machine.
- Train everyone involved in molding production with the right technique for ejector pin lubrication. This essential step will prevent excessive heat buildup or galling of the pertinent segments.
- More frequent and lighter grease application is preferable to over-applying. Resins that emit gases or contain flame retardant additives are known to reduce key release properties and require more frequent treatment of grease than those without such characteristics.
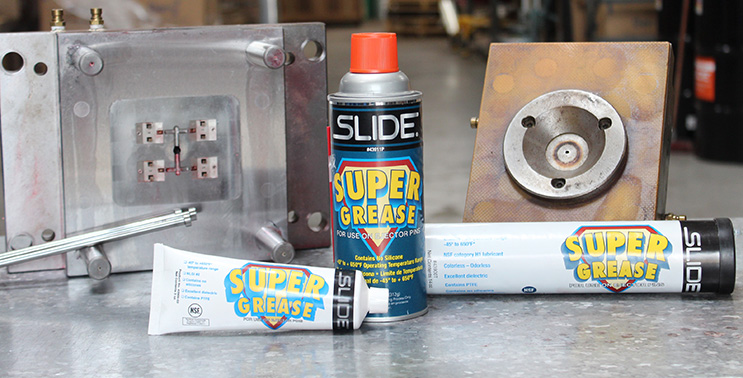
Slide takes pride in the superior functionality of its Super Grease – the only formulation of this type in their catalog. Choosing Slide Products also guarantees that none of the active pieces on your line will unfavorably interact with each other. Slide’s Super Grease is found across multiple industries including molding, manufacturing, agriculture, construction, transportation and provides real-time benefits.
The experts at Slide are always here to make your injection molding methods as proficient and effectual as possible. Solve your greasing issues with our 100+ years of factory field experience and Best Practices recommendations and schedule a future on-site visit as outlined in the Top Tier Service program.