March 7th, 2023
Investment wax casting is an important metal molding process that is widely used to produce complex parts with a great degree of accuracy and precision. This cost-effective method yields intricate designs that would be difficult or otherwise impossible to achieve with other manufacturing techniques. From the initial concept stage to the final production of the part, this blog will explore investment wax casting in detail and highlight what makes this operation so unique.
Step 1
The first step in the method is to create replica patterns of the parts that will be cast. This can be accomplished with a range of materials, such as wax or plastic, and is typically generated utilizing injection dies. Many characteristics of investment wax casting – such as smooth surfaces and specific detailing – are dependent on these dies. Each segment requires a separate configuration that will then be assembled to form the end product.
To make the whole procedure more efficient, Slide offers its fast-acting Silicone Mold Release formula. This heavy-duty solution can be sprayed onto the dye, allowing the mold to quickly disengage. Additionally, NEXGEN and Mold Shield solutions can help with cleaning buildup and preventing molds from rusting between runs.
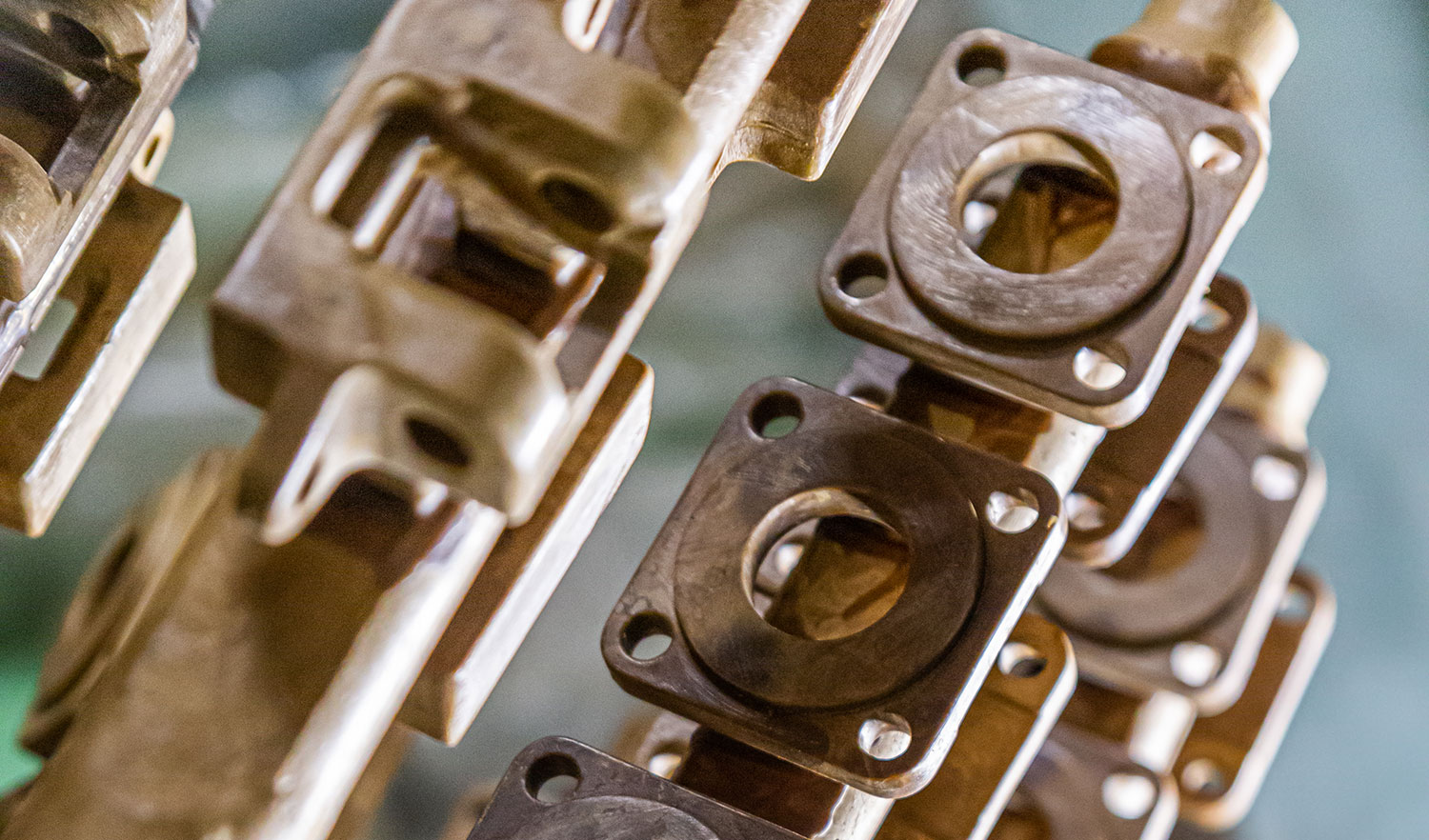
Step 2
Step two involves assembling the wax to a feed system called a sprue. The sprue not only holds the wax patterns but also forms a sufficient pathway through which metal can flow. This new group of attached patterns is called a tree. The structured piece is then utilized to craft the shell that replicates the exact detail of the desired casting.
Step 3
The next step is to create a ceramic overlay. This is achieved by making ceramic slurry (mixture of fine particles suspended in water) then repeatedly dipping and covering the prototype until a thin layer coats it. Subsequently, the material will harden and form the shell.
Step 4
Once the ceramic shell has been created, the wax tree is removed by melting or burning it out of the enclosure. This leaves a hollow cavity that is an exact duplication of the part to be used as a mold. When ready to be filled, the shell is then heated in a furnace to temperatures hot enough to allow melted metal to flow freely within.
Step 5
The final step in the progression is to construct the finished part. Molten metal is poured into the mold and allowed to cool and solidify. Once cooled, the ceramic shell is broken away from the casting, leaving the completed project. The casting is then cleaned and polished to remove any excess metal or imperfections.
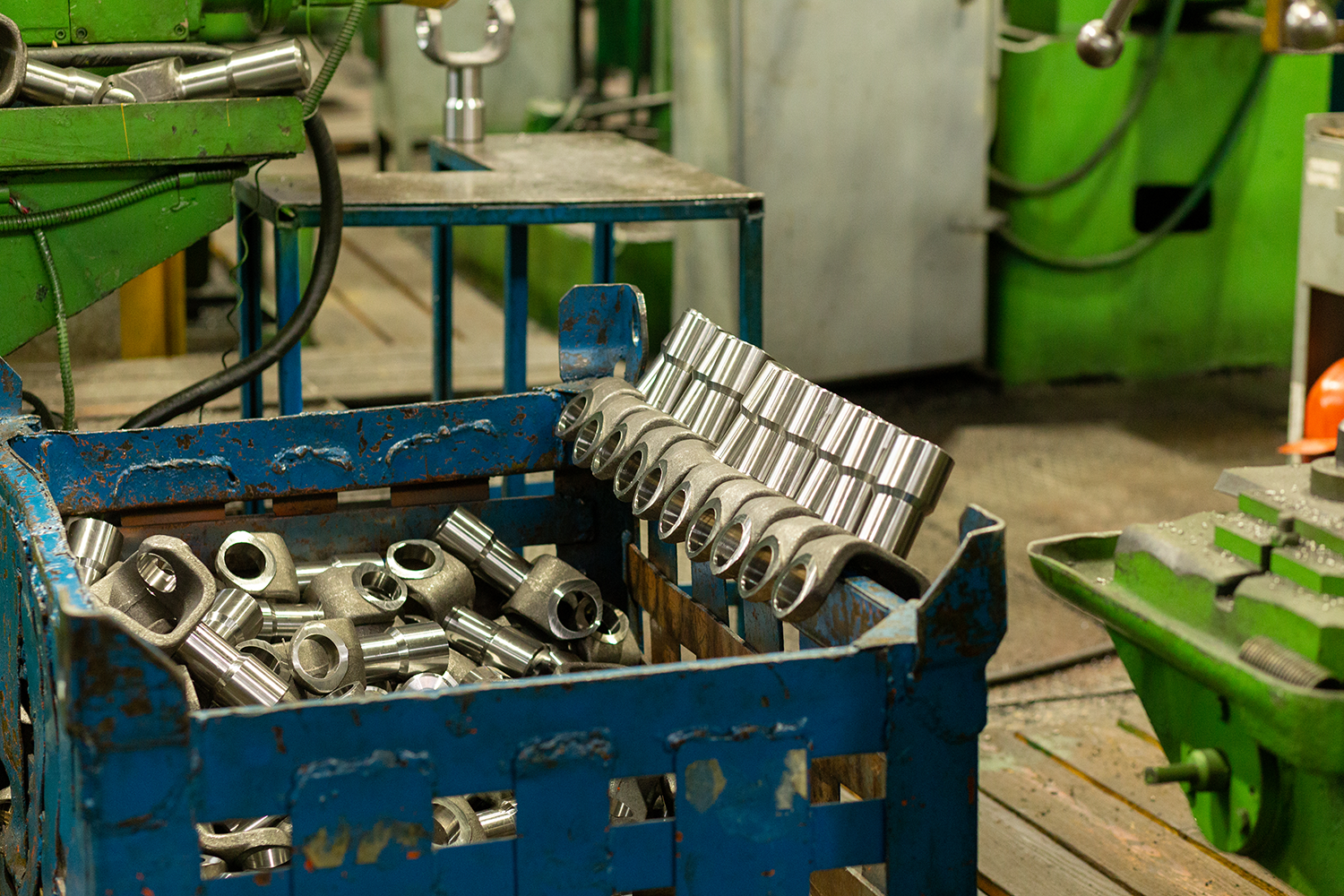
Investment wax casting has many benefits with the most notable being that it allows for the creation of complex shapes with extreme accuracy. This makes it an ideal technique for intricate designs and pieces that require total precision. Products that are commonly made from investment wax casting are medical equipment, firearm components, gears and jewelry.
Another notable benefit of investment wax casting is that it can be used to fashion parts from a wide range of metals including steel, aluminum, bronze and titanium. This versatile method is ideal for manufacturing small to medium-sized production runs.
The process can have some real limitations, however. It can be time-consuming and does require a high degree of skill and expertise to achieve the desired level of accuracy and exactitude. It is also not well suited for large production flows, as the cost per part can be greater than with other manufacturing practices.
Despite these drawbacks, investment wax casting remains a popular and useful approach for producing high-quality precision parts. The benefits outweigh any disadvantage in using the popular molding technique. It remains in the forefront as the best option in many applications. See Slide’s product offerings for the Investment Wax Casting industry.