October 22nd, 2024
A Modernistic Material – Plastic
When we think of inventions, we often think of airplanes, computers, cars and other discoveries that have transformed our daily lives. However, we frequently overlook the multifaceted manufacturing processes, design applications and materials their production entails. Most people don't consider the tools and methods that have brought these revolutionary ideas to fruition.
When it comes to manufacturing, plastic is one of the most predominant mediums for modern engineering, offering high-quality outcomes at a quick pace for an affordable price. The advent of injection molding techniques has elevated the design and implementation parameters for these materials. Without the use of this process, many industrial innovations and new-age technology would not exist. Let’s glance over the history behind the groundbreaking approach that powers today's world of mass production.
Early Plastics – Thermoplastic
In 1856, the first man-made thermoplastic, known as Parkesine, was invented by metallurgist Alexander Parkes. This synthetic formulation was made up of cellulose nitrate and various solvents. Parkesine was a transparent, flexible polymer that could be shaped, molded and colored when heated, then cooled to a hard, durable composition. This laid the groundwork for the widespread use of plastics in the modern manufacturing realm.
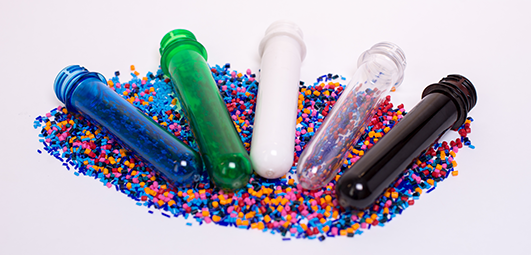
The Rise of Plastics – Revolutionary Discoveries
Brothers Isaiah and John Hyatt created the first injection molding machine in 1872, initially made to make buttons, combs and other small items. Although these devices could be facilitated for production, they also posed an issue of high flammability. In 1903, German scientists Arthur Eichengrun and Theodore Becker improved upon this development and created a soluble form of cellulose acetate, which was less flammable than previous materials. Following after, there was a progression to several thermoplastics being, which broadened the range of potential usages. Many of the most popular thermoplastics like PVC, polystyrene and polyolefins were invented during this time (early 1900s).
World War II – Needs for Mass Production
The dramatic shift in the need for goods during World War II necessitated a growing demand for inexpensive, lightweight equipment on a mass scale. This led to a dramatic progression for the plastics industry. These advancements powered the first stages of high-volume post war industrialization.
The war disrupted rubber supplies due to attacks on shipping routes to Asia, while the demand for materials to build military equipment like tanks, placed an immense pressure on metal resources. As metal became scarce and costly, plastic acted as a viable substitute. As it became more popular, the manufacturing techniques advanced accordingly. Due to the affordability, durability and rapid output, plastic injection molding became a fundamental practice across numerous markets.
First Extrusion Screw Injection Molding Machine
By 1946, the first extrusion screw injection molding machine was invented by James Watson Hendry. He used a rotator screw to control the process and it evolved in the development of the first gas-assisted injection molding machine – subsequently starting the innovation of long, complex parts. This mechanical discovery revolutionized the process by enhancing the quality of components and remains a standard in machines today.
Commercialization – Polypropylene
In 1956, a cost-effective and versatile plastic material development known as polypropylene marked a considerable advancement in polymer science. This transformed the industry by being a fundamental component due to its melting behaviors, strength and ability to flow through molding processes. Polypropylene became widespread across plastic injection molding and contributes to many daily use products such as food containers, cars, packaging and more.
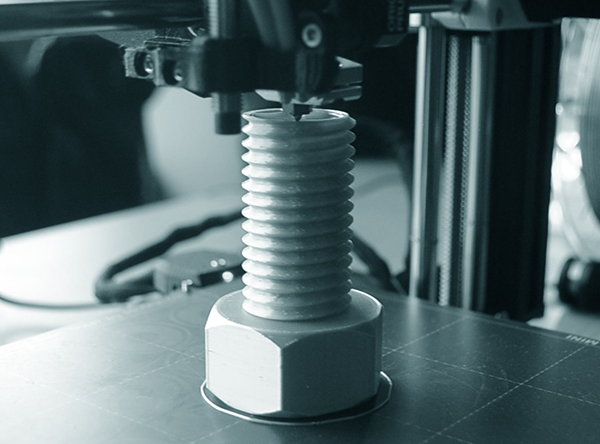
Computerization – Progression in Technology
During the 1970s and 80s, CAD (computer aided design) technology reshaped the design process by enabling complex shapes and improved molds. At this time, the rise of automation helped with making large-scale projects more feasible by increasing output speeds and consistencies. Designers could visualize a final product before any physical production began.
Broadening Advancements – Setting Standards
From the 1990s onward, more sophisticated techniques – particularly the introduction of 3D printing – helped to protect against potential problems. Efficiency standards and precision grew from the use of evolving automation and manufacturing tech. 3D printing, rapid prototyping and simulation software allowed for quick production, reduced waste and facilitated quality control.
Injection Molding – Contribution to the Modern World
Plastic injection molding has granted a transformative means for manufacturing worldwide, providing distinct advantages for specific applications. Key industries, such as automotive, medical, electronics and food/beverage, have benefited significantly from this process, enabling the creation of high-performance, durable goods.
Injection molding has greatly influenced product design, material inventiveness and automation. With continuous technological advancements, plastic injection molding is set to remain a cornerstone in production of diverse products, driving both innovation and efficiency in the manufacturing sector.