March 21st, 2023
Electric vehicles (EVs) are gaining popularity worldwide due to their environmental benefits and reduced operating costs. As more consumers choose to switch to these eco-friendly alternatives, the plastics industry has been able to profit from the new opportunities EVs have created in more ways than one. Here are seven examples in which the growth of electric vehicles is opening doors for plastic manufacturers.
1. Lighter weight materials
Because of their heavy batteries, EVs require lighter components to maximize their range and keep their overall weight down. Plastics are a perfect material for this purpose as they are much lighter than more traditional mediums such as steel and aluminum. In recent years, plastics manufacturers have been working to develop new lightweight parts that will improve electric vehicles’ overall efficiency.
2. Increased demand for batteries
As the demand for electric vehicles increases, so does the need for applicable batteries. Many of these are made using plastics in their casing as well as other essential components, such as polymer electrolyte membranes (PEMs). This is creating new opportunities for the plastics industry to innovate and design new products specifically for use in batteries.
3. Improved safety
The complexity of EVs requires high-performance materials that can withstand extreme temperatures and provide superior safety. In many cases, plastics are uniquely suited as they can be engineered to provide infallible strength and durability. Plastic manufacturers are always working to produce quality parts that can offer even greater protection for drivers and passengers.
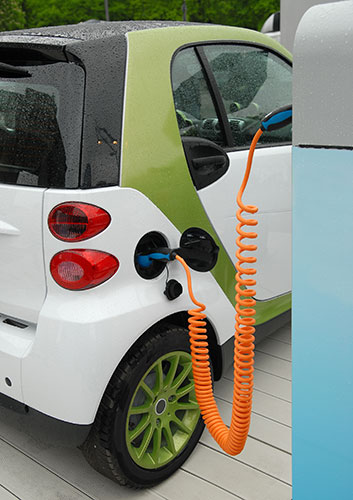
4. Cost Savings
Electric vehicles are becoming less expensive due to the decline in the cost of power source technology. To keep them affordable, EV makers are focusing on processes to help reduce operation and production costs. Oftentimes this means turning to the plastics industry. In response, plastic manufacturers are answering the call to make electric vehicles more accessible to all consumers.
5. Customization
In a highly competitive market, EV producers are striving to stand out from their competitors. To do so, they are understandably looking to plastic manufacturers to craft customized lightweight yet versatile pieces that can be incorporated into the vehicle and not hamper its performance.
6. Charging components
EVs require specialized charging infrastructure including vital connectors and cables, making plastic components the ideal choice. Plastics companies have developed state-of-the-art EV charging constituents to be durable, waterproof and resistant to chemicals as much as possible. These parts have been generated to hold up in all climates and are considered safe and reliable.
7. Interiors
The interiors of EVs require a different approach than traditional cars. Plastic manufacturers can help meet these new requirements by fabricating sustainable, recyclable and eco-friendly materials. This is leading to the development of plant-based plastics and other biodegradable equipment that can be used in EVs to reduce much of the environmental impact that may occur.
For these reasons and more, electric vehicles are providing plastic manufacturers the ability to revolutionize and create innovative solutions, sustainable growth and strong ties between automobiles and plastics makers. As the popularity of EVs is expected to continue its meteoric rise, we see plastics as vital in holding vehicle prices down and staying within reliable safety standards for all consumers.