February 18th, 2025
In the plastics industry, designing for manufacturability is a process in which molders optimize part design to reduce production costs, tackle potential defects and shorten cycle times. It is a crucial element that helps to identify existing and potential problems that may occur during fabrication. The goal of DFM is to deliver the greatest level of satisfaction at a lower cost for greater profit. Below, we will cover some of the main points that are used to support DFM.
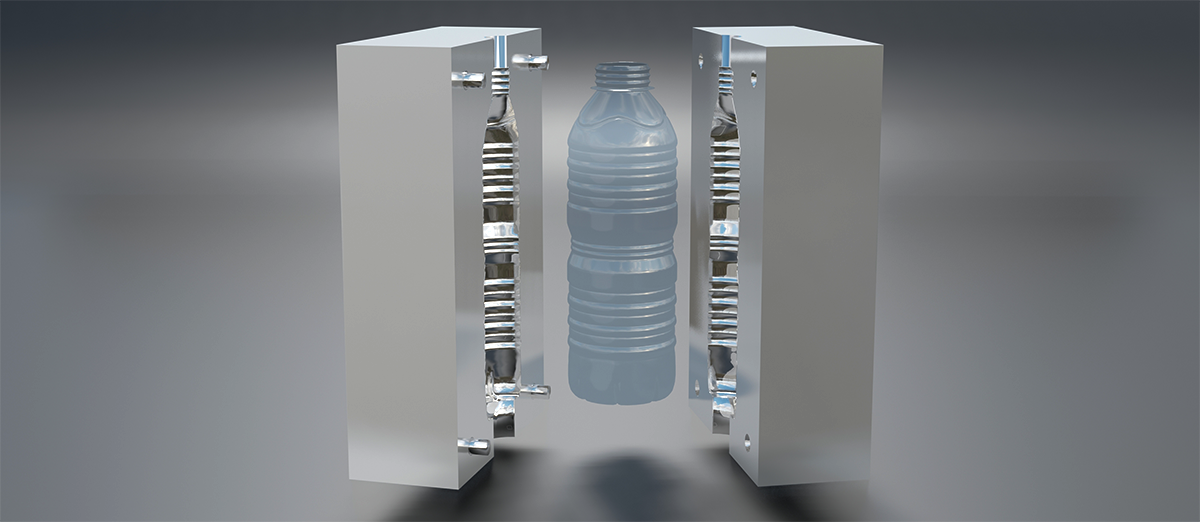
Part Complexity Considerations
Simplifying your design not only lowers material and tooling costs but reduces the risk of defects.
- Uniform Walls
To minimize the risk of uneven cooling, warping and sink marks, you should certify wall thicknesses are uniform. This sanctions a smooth transition for an even flow inside the cavity. Rounding corners alleviates pressure associated with sudden changes in density and improves overall structural integrity. - Draft Angles
These help to create space for parts to efficiently release by forming parting lines with minimal resistance. Adding an angle to the vertical surface of a mold cavity ensures a proper draft for an easy release. - Radii and Fillets
Abrupt cuts complicate molding production and add stress concentrators. Radii and fillets, (smoothing or rounding out sharpness), expands flow and is vital to upholding part structure. Fillets distribute tension over a broader area lessening the probability of outcome failure.
Flow Optimization
Finding ways to fully optimize the flow of composites helps to fill molds entirely to avoid dimensional errors.
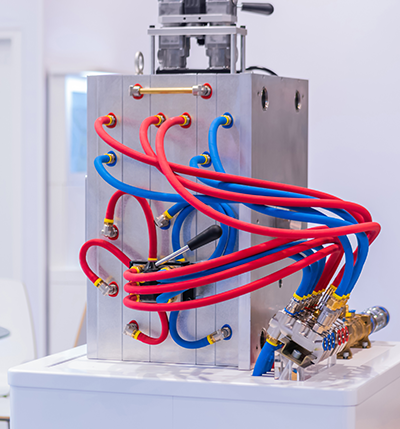
- Gate Location
The placement of gates influences run patterns, quality and material usage. To avoid interference with a parts function or appearance, position gates near the thickest section of the mold – this should allow for stable dispersal. - Avoid Marks
When material flow is disrupted, marks and weld lines may appear. Controlling the runner system and gate will eliminate those anomalies. Prevent them from happening by adjusting temperatures, injection speed and pressure for a smooth surface finish. - Cooling Channels
Uneven cooling can lead to warping, residual stress and dimension inaccuracies. Strategically placing channels helps to create an even cool and reduces cycle times. Molds should follow the shape of the intended design as closely as possible.
Material Selection
There are unlimited options of hybrid materials, additives and fillers available, but only a handful can be used in specific plastic injection molding methods.
- Compatibility
Each composite has unique characteristics, so choosing the right one can supplement proper performance, lower cost and ease molding. Your machine and chosen material should be synchronized to avoid production issues. - Properties
Material selection needs to match the required resistance, impact endurance and flexibility of the product. It’s important to explore and compare relative mechanical properties, including shrinkage, flowability and durability to make the right choice. - Alternative Composites
As sustainability is at the forefront of the plastic manufacturing focus, considering recyclability is encouraged. There are various options that allow for reusability to reduce waste and minimize expenditure.
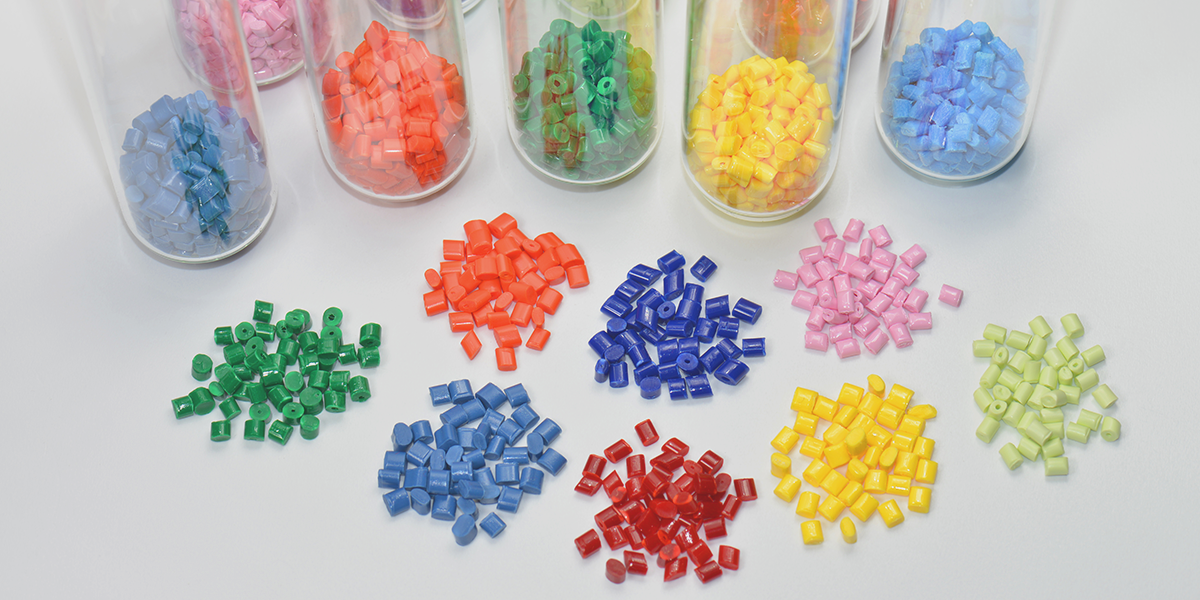
Early Involvement
Close work between mold designers, engineers and specialists early on ensures both function and aesthetics are in check.
- Communicate with Tool Suppliers
Initially involving mold makers in the design process allows manufacturers to identify problems and feasible strategic aspects. They can give feedback on features that may cause difficult tooling or are too expensive to produce. - Cost Plan
Collaboration among teams provides a more accurate cost estimate for both tool design and part production. Designers must consider complexity, cycle times and other variables that can affect the bottom line. Having the entire group engaged induces better budgetary planning and decision making. - Leveraging Technology
Using software to assist with simulation and prototyping is helpful in predicting problems such as air traps, short shots and excessive material usage. Mold flow analysis, 3D prints, AI and real time monitoring augment review processing parameters before mass production.
Integrating DFM into plastic injection molding manufacturing practices is important for generating high quality parts that will meet both customer and expense estimates. While the actual production aspects matter, real efficiencies of time and budget rely heavily on the developmental phase – where objectives are clear, and surprises can be avoided. Whether you are working on a new part or updating an existing one, being mindful of the “big picture” is vital.
Looking for expert advice on how to fully optimize your production? Contact the experts at Slide – we can help meet your specific needs!