December 17th, 2024
Injection molding is one of the most efficient manufacturing methods for creating high volume repeatable parts. But as with any process, producing quality output requires proactive risk management and attention to every phase. With so many details involved, due diligence ensures standards are met, from design concepts to proofing stages. Failing to take preventive measures can lead to subpar product quality and major financial losses. Below is a brief overview of some of the most common defects, causes and steps you can take to prevent them.
Flow Lines
Appearing as a wavy pattern of lines on the components exterior, flow lines are often a different shade from the intended molded component. These are usually seen near more narrow sections, like the entry parts of the mold. The integrity of an original design isn’t compromised but the cosmetic aspect of a resulting outcome is negatively impacted.
Common Causes
- These imperfections often occur when liquid molten plastic inside a mold’s cavity meets the polymer that has already cooled. Differences in wall thickness can impact the rate of cooling and contribute to flow lines.
Remedies
- Increase injection speeds, pressure and temperature to ensure proper filling.
- Round off thicker corners to keep a consistent flow rate and prevent premature cooling.
- Increase the diameter of nozzles to raise the flow rate.
Surface Delamination
This condition is labeled as defects that transpire on a part’s surface which separates it into thin, peelable layers. More than just a cosmetic issue, these can reduce overall part integrity.
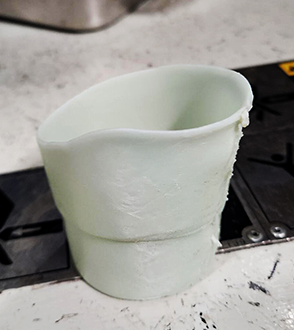
Common Causes
- Delamination can come about when contaminants such as mold release agents or moisture are present on the material preventing proper binding. Using polymers that are not chemically compatible heightens the risk of delamination.
Remedies
- Ensure compatibility of all polymers in use.
- Increase the cavity temperature.
- Smooth corners within can discourage sudden changes in melt and flow.
Sink Marks
These deformities are characterized as small recesses or depressions that present on flat surfaces on a molded part. They occur when the inner part shrinks and pulls the outside material inwards.
Common Causes
- When a polymer cools too slowly, it triggers shrinkage and leads to depressions. They most likely will take place in thicker areas of a product and are commonly usually seen on items with varying wall thicknesses.
Remedies
- Increase internal holding pressure by lowering injection speed and time.
- Allow further cooling time to let resin form a proper skin.
- Use thinner walls in your design to allow for quicker cooling near the surface.
Warping
Deformations that arise when components unevenly shrink are known to cause warping. If regions of the mold are cooled at various rates, it induces stress that results in disfigured structures.
Common Causes
- The main factors for this occurrence include the type of material used and the molecular characteristics as each reacts differently to temperature fluctuation. Uneven temperatures create internal strain and distort material.
Remedies
- Select the right material before starting the process; semi-crystalline is more likely to warp than amorphous polymers.
- Reinforce polymers with fiber to prevent expansion or contraction.
- Allow for parts to cool properly at a sufficient gradual rate.
Weld Lines
Also known as knit lines, they often come about when two flows of molten resin meet at different temperatures. These are commonly shown on edges, corners and angles.
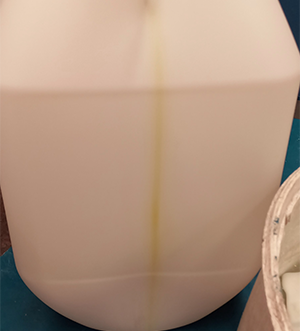
Common Causes
- They frequently form due to an insufficient temperature allowing for improper bonding.
Remedies
- Maintain consistent flow rate with adequate back pressure.
- Use a higher quality plastic with fewer impurities.
- Increase the melting temperature to avoid partial solidification.
Jetting
When resin enters the cavity too quickly, cooling before the whole cavity is filled, it leaves snake-like squiggly folds on the product’s surface.
Common Causes
- This problem often arises when the resin is pushed against the mold too forcefully, thus hurting the integrity of the part by lessening the durability of the finished product.
Remedies
- Temperatures for the barrel and nozzle should be adjusted to be more controlled.
- Choose a lower-viscosity plastic to sanction a more gradual and uniform fill.
- Use a larger gate size to ensure greater contact between all elements.
Despite the efficiency and versatility injection molding provides to the world of manufacturing, its complexity means various defects are prone to emerge. While this list covers a handful of many issues that come about during the process, these are some of the most frequently encountered. Being attentive to regular maintenance, monitoring control parameters and optimizing design can help ensure a final product with high quality, resilient items.