August 20th, 2024
Because product design and quality specifications need to be met every single run, color plays an integral role in the injection molding industry. With several different methods with which manufacturers can approach, this leaves plenty of room for error. Not adhering to best practices will ultimately lead to poor outcomes, fuel counterproductive misconceptions and cause unnecessary frustrations. Therefore, understanding these inconsistencies and the best technique for ensuring color uniformity can help produce high-quality, visually appealing parts, time after time.
Myth 1: Any Color Can Be Achieved Easily
Reality: Theoretically, while any color can be formulated, obtaining the exact shade desired could prove challenging. Direct correlations exist between different materials, pigments and processing conditions. A final tint is influenced by a myriad of factors such as: base resin color, types of dye used and molding process parameters. Achieving a specific hue often requires significant expertise/training, exacting science and thorough testing.
Myth 2: Once the Color is Formulated, It Will Always Be Consistent
Reality: Color matching and precise invariability in injection molding depends on certain dynamics such as raw material variations, managing appropriate settings and environmental aspects. Even slight alterations in the resin supplier, batch or additives might translate to noticeable changes. Regular monitoring and adjusting are required to maintain stability throughout the entire operation.
Myth 3: Adding More Pigment Improves Color
Reality: Injecting more pigment occasionally brings out a deeper color, but causes other problems like uneven distribution, increased material costs and potential stress on the physical properties of molded parts. It’s essential to pinpoint the optimal pigment loading for the desired color without compromising the end result.
Myth 4: Masterbatches and Liquid Colorants are Interchangeable
Reality: Masterbatches (solid concentrates) and liquid colorants serve similar purposes but have different compositions. Masterbatches are easier to deal with and deliver more consistent color, though mandate utilizing higher temperatures to disperse properly. Liquid formulas are more economical for small runs but may require specialized equipment and handling procedures to avoid contamination and warrant uniform mixing.
Ensuring Color Consistency in Molded Parts
Color precision in injection molded parts necessitates skillful consideration that encompasses raw material selection, operational control and quality assurance. Below are several important highlighted steps on maintaining a careful balance:
1. Raw Material Choice and Management
- Consistent Resin Resource: Use the same grade and supplier for resin to diminish variability. Disparities in resin properties can affect color output.
- Correct Storage: Store resins and tints in a controlled setting to prevent impurities and degradation. Moisture and temperature fluctuations can change it substantially and create disruption to the color.
2. Colorant Selection and Preparation
- Choose the Right Product: Select an applicable type of dye (masterbatch, liquid or powder) based on usage and desired outcome.
- Mixing and Dispersion: Ensure thorough mixing of colorants with your base. Poor distribution can lead to unwelcome marks and color destabilization.
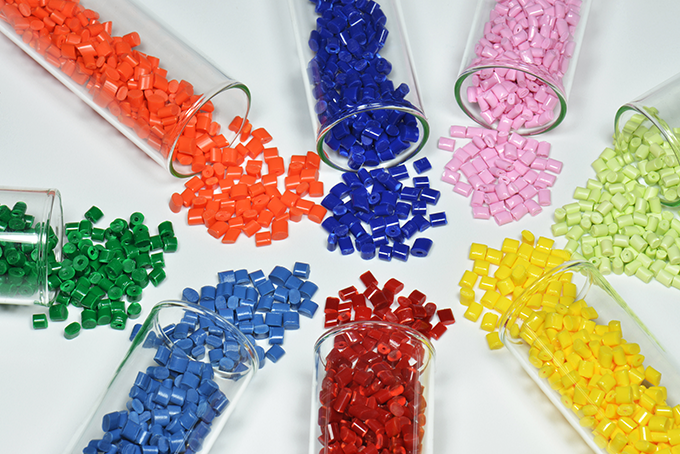
3. Process Control
- Machine Calibration: Regularly calibrate injection molding machines to remain at the perfect settings. Deviations in temperature, pressure and cooling values could have an adverse effect on color.
- Steady Processing Parameters: Maintain regulation once ideal limits are determined. Record and monitor manufacturing conditions and cycle periods.
- Real Time Monitoring: Use sensors and monitoring to detect and correct deviations immediately. Automated systems will aid in preserving quality.
- Proper Cleaning: Prevent build-up and other unwanted contaminants by cleaning machines routinely. Using products like Slide’s Mold Cleaner 4 ensures molding machinery can perform optimally especially when it comes to color transfer.
4. Quality Assurance
- Color Measurement Tools: Use measurement instruments, such as spectrophotometers, to objectively assess color reliability. These tools can detect subtle variations that may not be visible to the naked eye.
- Sample Testing: Regularly test samples from production runs to compare against master color standards.
- Batch Documentation: Keep detailed records of each batch, including raw material lot numbers, processing criteria and test results. This documentation helps identify and address sources of discrepancy.
5. Continuous Improvement
- Feedback Loop: Establish a feedback loop with production and quality control teams to continuously tweak color techniques. Encourage open communication and collaboration.
- Supplier Partnerships: Work closely with resin and colorant partners to address any concerns, thus safeguarding that you are receiving premium raw materials.
In conclusion, color injection molding is a complex method influenced by multiple elements, and attaining dependable outcomes calls for vigilant attention to every aspect throughout the process. By debunking common fallacies and applying a systematic approach for material selection, operational maintenance and quality assurance, manufacturers can produce superior, visually coherent molded cuts repeatedly.
No matter what injection molding obstacles your company may be experiencing, Slide is here to support you! Reach out to an expert today to learn how we can help meet your color molding needs.