November 21st, 2023
Injection molding is a widely used manufacturing process that has revolutionized the way we produce plastic and metal parts. From everyday consumer products to complex industrial components, this technique has a vast range of applications. Subsequently, a successful production outcome does rely heavily on utilizing the correct injection mold itself.
Below, we will explore the various kinds, categories and sizes of molds and delve into why making an informed decision when selecting one is central to turning out the perfect product.
Single Cavity
Single cavity molds have one space into which plastic resin can be injected – creating a single item per cycle. Since a more simplified design set-up is often used, lower manufacturer costs often result making these molds ideal for small-scale yield and prototyping. Additionally, single cavity molds enable precise monitoring of molding parameters and are suitable for complex part geometries. While this method is slower than most others, the molds are invaluable for constructing intricate pieces with high precision.
Multi-Cavity
With many areas into which plastic resin is injected, multi-cavity molds allow for numerous parts to be created simultaneously. For operations where large amounts are needed within a fixed time frame, these molds are best-suited.
Nevertheless, multi-cavity molds call for a larger upfront investment over single-cavity and can prove somewhat risky. This methodology requires additional lead time since it takes longer to form simultaneous parts. In addition, an added level of maintenance is essential because if one cavity malfunctions the entire mold becomes unusable.
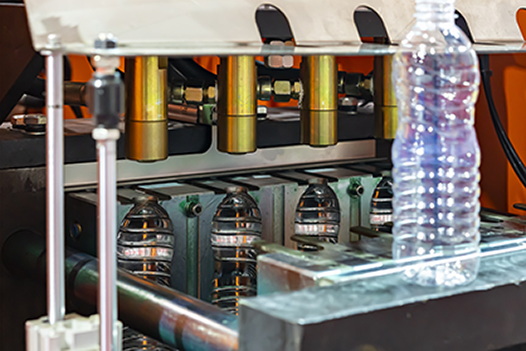
Hot Runner
Hot runner molds have an internal heating system that is designed to maintain the molten plastic at an elevated temperature as it flows through the mold base. This affords molders some significant advantages over other means such as reduced waste, faster cycle runs, and decreased production expenses. Hot runner molds are optimum where color changes or material conversions need to be implemented frequently.
One drawback worth mentioning is that hot runners are complicated and therefore costly to design and maintain. Technicians well-versed in temperature control are mandatory and molds may be subject to issues like color contamination. Even so, they are preferred for high-volume production where material savings and efficiency outweigh the initial investment.
Insulated Runner
A variation of hot runners, insulated runner molds, are composed from elements that keep the die at a controlled temperature. They are built to sustain the molten state of the plastic until it reaches the cavities. Avoiding any premature solidification of the polymer will minimize waste and improve cycle times.
A primary challenge is that Insulated runners also require precise temperature control in order to operate. Even so, they are very valuable for reduced waste operations and the need for meticulous consistency.
Cold Runner
Cold runner molds are essentially the opposite of hot runners. A systemic coagulation happens within it during a fabrication sequence, resulting in spoilage that needs to be removed and/or recycled. CRs are simpler than other molds and start at a lesser price point in addition to ease of maintenance.
Disadvantages: The removal of runners adds to the whole course of action resulting in elevated expenditures, and a slower methodology. Despite that, it’s usually a budget friendly reliable answer for many applications.
Two Plate
Two plate injection molds consist of both a cavity plate and a core plate. The cavity plate holds the hollow part of the mold which shapes the final product. The core plate contains the mold’s center, which helps fashion the inner features of the part being produced. These molds are less complicated than other varieties, which leads to lower start-up costs.
Disadvantages: Two-plate molds would have lengthier run cycles and might not be appropriate for parts with elaborate shapes and patterns. Ejection mechanisms may also be more challenging to implement, which is likely to impact quality of the output.
Three Plate
Similar to two plate molds, these feature the addition of a runner plate that separates the mold into two halves, allowing for more complex geometries and streamlined ejection. This makes it easier to remove sprues, runners and finished pieces without the need for additional slides or side actions.
Three plate molds are best for intricate parts and can reduce the risk of damage during ejection. However, they are more complex and expensive to manufacture and maintain than more basic molds.
Stack
Stack molds consist of multiple layers of plates and used when different parts or coatings need to be turned out concurrently. These are meant for developing sophisticated pieces with diverse elements, colors or textures in distinct layers. Using a stack mold can increase production proficiency and have the capacity to process sections all at once, as multiple layers are formed in a single shot.
Stack molds are technically intricate but often pricy to build and maintain. Working with them necessitates a specialized understanding of precise management over material temperatures, injection pressures and mold movements to ensure proper layer adhesion and quality.
The Final Choice
Cost efficiency, product quality and run time are just some of the reasons that make finding the right mold so important to your business. By knowing the choices out there and their appropriate applications, an informed decision can be reached that aligns favorably with your production needs.
Still not sure which injection mold is right for you? Slide is always available to contribute our expert input. With years of experience and research, we would be happy to provide advice to help make your injection molding processes as efficient as possible.